The DIGIMU consortium, handled by MINES ParisTech and Armines, is supported by the CEA and the ArcelorMittal, Aperam, Framatome, Constellium, Aubert & Duval, Safran, Ascometal, Timet, and Transvalor companies
What is the aim of DIGIMU?
DIGIMU aims to develop an innovative global framework for the simulation of microstructural changes during forming processes.
It is also the name of the software developed by the company TRANSVALOR in collaboration with the CEMEF and industrial partners of the DIGIMU Chair (2016-2021), RealIMotion Chair (2022-2027) and consortium, which was first released commercially in 2016. This software is based on numerical developments in metallurgy made by the MSR (Metallurgy Structure Rheology) CEMEF MINES ParisTech team. All the numerical developments of the consortium contribute to the development of this software.
Why DIGIMU?
One of the European Union’s objectives in climate change consists of reaching net-zero greenhouse gas emissions by 2050. Such perspective puts the metallic materials industry, as a large contributor to carbon emissions, under tremendous pressure for change and requires the existence of robust and qualitative computational materials strategies to design, to enhance, to calibrate, with a very high degree of confidence, new metallic materials technologies with a limited environmental impact. From a more general perspective, the in-use properties and durability of metallic materials are strongly related to their microstructures, which are themselves inherited from the thermomechanical treatments.
Hence, understanding and predicting microstructure evolutions are nowadays a key to the competitiveness of industrial companies, with direct economic and societal benefits in all major economic sectors.
Multiscale materials modeling, and more precisely, simulations at the mesoscopic scale, constitute the more promising numerical framework for the next decades of industrial simulations as it compromises between the versatility and robustness of physically-based models, computation times, and accuracy.
In this emerging context of « digital materials science », the DIGIMU consortium has two main objectives. The first concerns the development of an efficient multiscale numerical framework adapted to these questions. The second relates to the optimization of these techniques in terms of numerical cost and their validation by the industrial expertise at the heart of the DIGIMU consortium. For these digital tools, which are still quite news, it’s a question of going beyond the usual framework of « simulation for industrialists » and moving towards « simulation by industrialists ».
Moreover, if the DIGIMU background is mainly dedicated to recrystallization and solid-solid phase transformations for metallic materials. The transverse numerical framework developed by the DIGIMU consortium presents also large potential for the modeling of numerous physical mechanisms occurring at the microscale and for a large range of materials (metallic or polymer composites, granular materials, …).
In this context, a breakthrough numerical strategy to describe the microstructure evolutions of metallic materials during complex industrial thermomechanical treatments has been developed through the ANR Industrial Chair DIGIMU (2016-2020). The outcoming DIGIMU software is now available for the industry, and able for quantitative predictions of microstructure evolutions on material volumes in the range of one mm3, with typical computation times of a few days when performed on a simple laptop. Such simulations and computational efficiency were a dream ten years ago, a reality now with the DIGIMU developments.
The purpose of the RealIMotion ANR Chair program obtained by the consortium in 2022 is to push the limits of numerical metallurgy further and develop a promising new numerical framework coupled with a machine learning physically-based strategy to aim for massive computations, consideration of much larger material volumes, in connection with macroscopic simulations and still with reasonable computation times to be compatible with industrial daily uses. Such a leap in the models will open the door for industrial partners to tune numerically thermomechanical routes, build microstructure-targeted processing maps and automatically propose new enhanced homogenized models. RealIMotion Chair program project brings the cutting-edge and exploding strategies of data science, physically-based models, and machine learning at the service of industrial metallurgy.
The French industrial consortium supporting the developments of digital materials in the context of hot metal forming has grown in the RealIMotion proposal. Constellium and Aperam are new partners. Framatome, Aubert&Duval, ArcelorMittal, CEA, and Safran brought new targeted applications on zirconium alloys, aluminum alloys, dual-phase steels, and new generation nickel based superalloys.
The students recruited in the RealIMotion Chair will enjoy a perfect environment to become experts in computational metallurgy, digital twins, and IA and meet the metallurgical industry needs for the future. The expected benefits will be job-creating for all the partners involved. The software integration of developments, through the provision of free access tutorials, has also a strong potential impact on teaching and the dissemination of the methods developed within training courses and laboratories specialized in metallurgy.
A recent DIGIMU illustration:
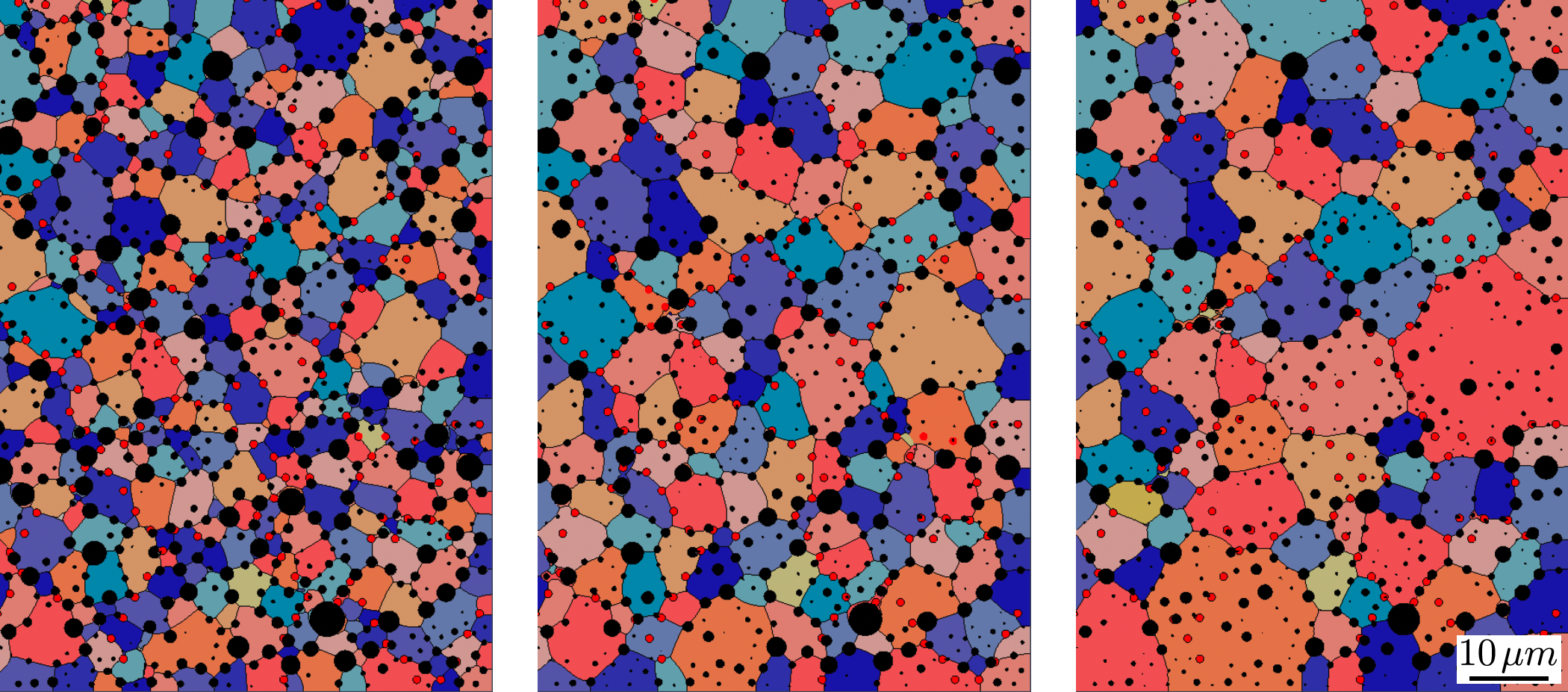
Illustration of a Digimu simulation concerning a thermal treatment applied to a nickel base superalloy and the modeling of the grain boundary network evolution while taken into account the dissolution of a second phase particle population in black and static oxides in red. PhD K. Alvarado – 2021